4 Common mistakes made in the RCA process
and
how to avoid making them
This month in Safety Review we focus on optimising the Root Cause Analysis process.
Our Safety Specialists identify common mistakes in RCA and provide guidance on how to avoid making them.
#1 Mistake:
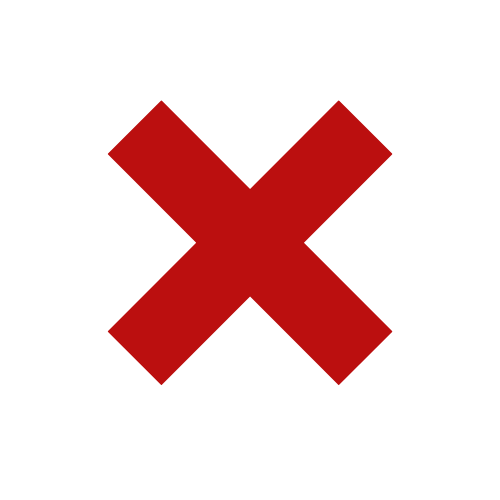
Caution: Inadequate investigation
A lack of detail, facts or evidence related to the initial assessment of the event.
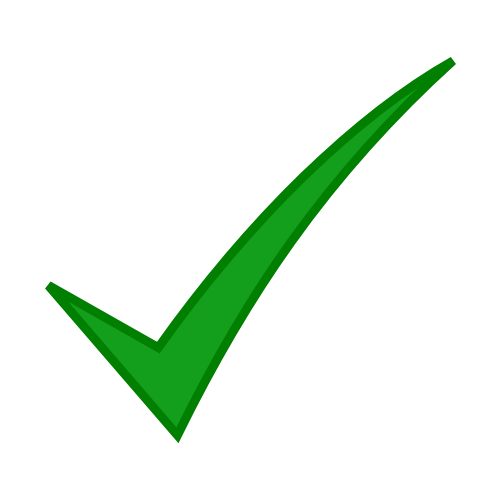
Control: Define the problem or event
Allocate sufficient time to investigate the facts and analyse the details to understand the “What” and “How” of the initial problem, before moving on to Root Cause Analysis.
#2 Mistake:
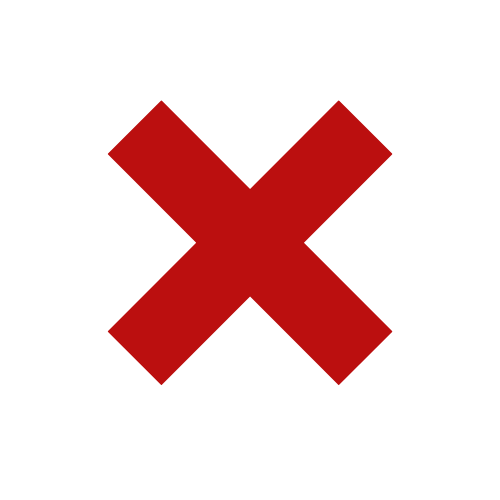
Caution: Insufficient validation
The incorrect distinction between the Root Cause and Contributing Factors.
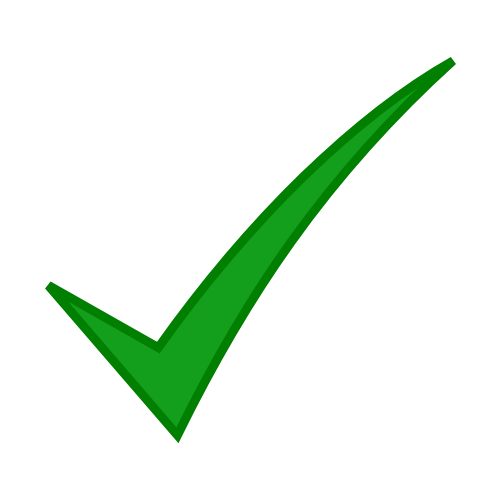
Control: Distinguish correctly between the Root Cause and Contributing Factors
When considering an environment with multiple contributing elements, defining the problem accurately will assist in determining whether the element is the Root Cause (primary) or a Contributing Factor (secondary).
#3 Mistake:
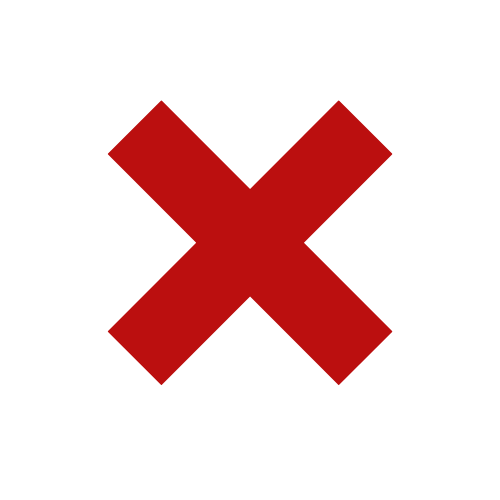
Caution: Scratching the surface
Not delving deep enough to uncover the real Root Cause.
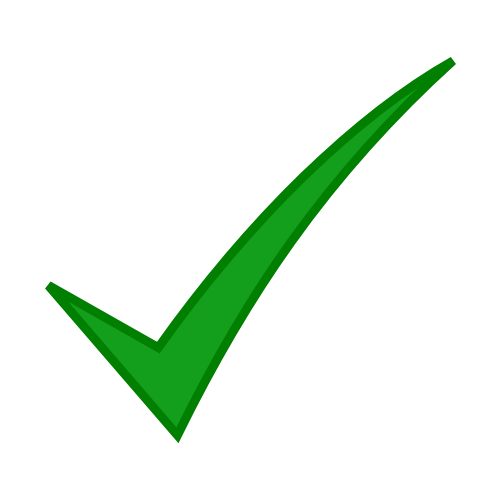
Control: Achieving a balance
It may be necessary to go one step further to identify the real Root Cause and prevent the re-occurrence of the problem. (Practice and experience make perfect). Identifying a training need, lack of leadership or management are typically not Root Causes. They are Contributing Factors with the real Root Cause to be found one step further.
#4 Mistake:
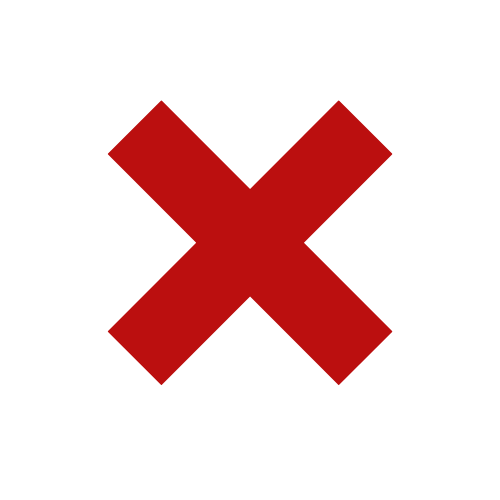
Caution: Inadequate corrective action
Not developing an effective corrective action plan/mitigation/control measure that addresses both the Root Cause and Contributing Factors.
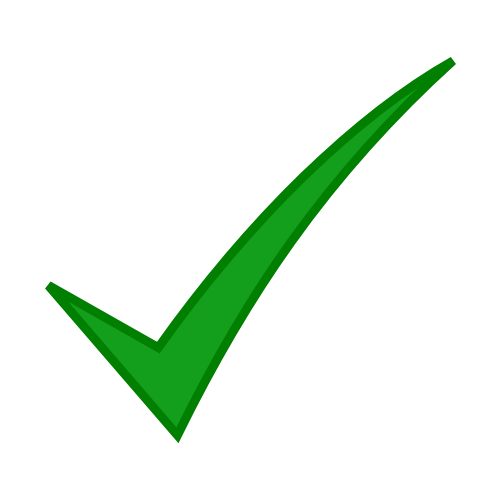
Control: Corrective action plan (CAP) with “gravitas”
The goal is to develop, implement and monitor appropriate corrective action that addresses the symptoms and the systemic failures to avoid a future re-occurrence of the event.