'UNDER WRAPS'
L&A’s Safety Specialists discuss
What are the safety concerns of vinyl wrapping of an aircraft?
By Allan Williamson
Table of contents
1. What is vinyl wrapping?
Vinyl wrapping is the practice of partially or completely covering a vehicle’s original paint with a vinyl wrap. It grew out of the automobile wrap advertising industry and has become increasingly popular as technology has developed, enabling complex graphics, designs and colour changes with relative ease.
2. Is it Safe to wrap an aircraft in plastic?
Of concern is the extension of the practice into the aviation industry, which began with composite and other light aircraft. It’s also being promoted commercially as an alternative to the traditional respray of larger aircraft for rebranding and livery change purposes. There are many claimed benefits which include speed of application, versatility of design, durability, cost, protection from the elements and weight-saving. However, there are also Safety concerns, which include extreme temperature variations, peeling, bubbling and aircraft corrosion.
Currently, there is not much information to be found in the aviation industry by way of regulations, standards and guidelines. This could be due to the variability of suppliers, materials and application techniques which are available and/or coming to market, as well as the liability issues that would arise should a wrap be implicated in an accident.
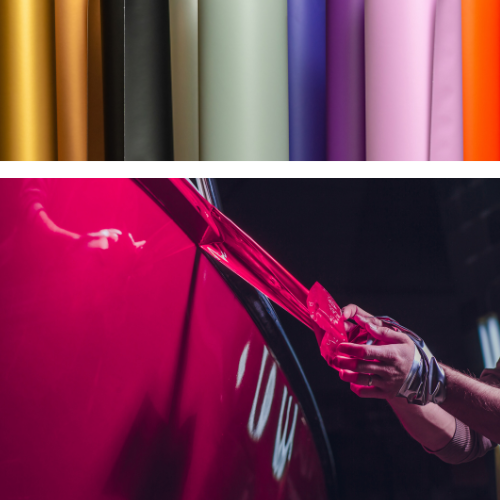
3. What are the Regulations?
3.1 EASA
EASA Information Bulletin no. 2018/03/5 “J-NEWS,” says the following regarding, Changes to External Livery with a focus on film layer application:
“Paint has long been used to protect aviation products, both for decorative purposes and to comply with requirements for external markings.
During recent years there has been a significant evolution in the application of printed film layers (sometimes known as ‘vinyl wrap’ or foil) to aviation products. However, there is little common industry-standardised guidance regarding the subject.
The broad range of benefits offered by using paint includes the provision of protection against erosion and general ‘wear and tear’ through to protection benefits more specific to the baseline materials used in the product design, e.g., protection against corrosion for some metals, or protection against UV damage for composite materials. Such benefits form part of the basis for certification and can contribute significantly to providing safety throughout the life of the product.
The generally successful history relating to paint application has been the result of effective paint material and process selection by the TCHs (Type Certificate Holders), appropriate communication of the acceptable associated maintenance actions by the TCH and the appropriate execution of these actions by the maintenance community.
An application for a change is required when external livery material and process, including the scope of its application to the product, is not addressed in existing applicable design data such as the SRM.
Application of a film layer over a significant area of the aircraft may require a major change approval or STC. Applicants for changes to external livery will need to demonstrate that applicable airworthiness requirements are not appreciably affected or have been addressed, and should consider the following points:
- Impact on ICA due to possible reduced ability to detect structural damage beneath the paint or film layer;
- Potential adverse effects of the use of a darker livery on structural properties;
- Mass balance and adverse effects on flutter characteristics;
- Adverse effects on underlying material due to chemical reaction;
- Adhesion of film throughout the flight envelope and effects of long-term deterioration;
- Impact on lightning protection;
- Static build-up leading to electrical discharge in or around fuel tanks or causing radio/navigation interference;
- Adequate instructions for the application of the film to avoid structural damage due to cutting tools or heat application and to prevent blocking or impeding emergency exits, static ports, fuel vents, air vents and drain holes;
- Required aircraft markings are maintained;
- Risk of loss of large parts of the film layer and interference with lifting surfaces, controls or engines;
- Revised or new ICA for maintaining the changed livery.
Examples of potentially impacted related Certification Specifications (CS 2X.—, where X varies according to the product):
CS 2X.305 Strength and Deformation, CS 2X.571 Fatigue (and Damage Tolerance) Evaluation, CS 2X.581 Lightning Protection, CS 2X.603 Materials, CS 2X.609 Protection of structure; CS 2X.611 Accessibility Provisions; CS 2X.629 Aeroelastic Stability (Flutter) Requirements, CS 2X.811 Emergency Exit Marking; CS 2X.1529 Instructions for Continued Airworthiness.
Finally, it’s worth mentioning that film layers (foils) are considered as parts and are therefore subject to marking requirements, as stipulated in Part 21 paragraph 21.A.804.”
3.2 FAA
The FAA has issued a policy memo available “on request” but quoted in the Small Airplane Issues List-ID A-101 on the subject: Vinyl Covering Shrink Wraps on Exterior of Part 23 Airplanes, Gliders, and Airships
Applicants should be aware that the FAA has issued a memo stating there are safety issues with the installation of vinyl-covering shrink wraps on the exterior of aeroplanes, gliders, and airships that are not present with other exteriors such as paint and de-icing boots.
These issues include hazards that are major to catastrophic, so the installation by FAA Field Approval is not acceptable. Only a Federal Aviation Administration (FAA) Type Certificate (TC), Amended Type Certificate (ATC), and Supplemental Type Certificate (STC) are acceptable for this installation. This memorandum is not applicable to vinyl decals or logos that are placed on limited areas of the fuselage or empennage.
The following are safety concerns with the installation of vinyl shrink wrap coverings that must be evaluated by the applicant for any TC/ ATC/STC application:
- Without proper engineering evaluation and/or tests, vinyl shrink wrap cannot be placed on any control surface or control surface tab: a. without consideration of the effect on the flutter characteristics (whether the surface is mass balanced or not) and b. where that installation would change the existing clearance between adjacent surfaces with and without loading.
- Scoring the skin of aircraft when cutting the vinyl sheets to fit, which can start cracks, particularly in pressurized aircraft.
- Blocking of fuel vents, static ports, hinges, drain holes etc., making them inoperative or changing the airflow over static ports.
- Use of an open flame from a blowtorch to apply the material. This is a concern around fuel tanks and vents, sensitive antennas, and especially on composite parts, which have cure temperatures well below the temperature of a blowtorch.
- Covering required exterior aircraft markings and emergency exits.
- Vinyl sheets losing adhesion on the surface or on rotating parts and jamming control surfaces or compromising engines.
- Static build-up causing electrical discharges in or around fuel tanks and causing radio/navigation interference.
- Tinting of windows and windshields with transparent vinyl, which compromises the view of pilots.
- The impact on removal of ice build-up on critical surfaces.
- Flammability of the material, including lightning strikes, and especially near engine exhausts and around engine nacelles. Flammability test specimens should be built up from the cowling/nacelle with the vinyl shrink wrap applied.
- Peeling of the wrap from rain or hail.
- Masking of cracks and corrosion in structure and skin.
- Lifetime of a vinyl shrink w/Tap installation. How long before mandatory removal.
- Effects of de-icing fluids on the film.”
4. Conclusion:
Before proceeding with an aircraft wrap, it would be prudent for an Operator to carry out a proper and detailed hazard identification and risk analysis, determine whether an STC or other approval is required, the qualifications required of the installer as well as the materials and procedures to be used, and the ongoing maintenance requirements.
5. References:
- Vinyl Frog ( 2023,15 March) Vinyl Wraps For Airplane
https://www.vinylfrog.com/blogs/car-wrap-tips/vinyl-wraps-for-airplane
- Dr. Marcelo Hirschler, (2017) GBI International, Consultant of The Vinyl Institute | Fire Properties of Polyvinyl Chloride
https://www.vinylinfo.org/wp-content/uploads/2018/12/Fire-Properties-of-Polyvinyl-Chloride_0.pdf
- EASA_J-News (2018 December) Item 2018/3/5 Changes to External Livery with focus on film layer application
https://www.easa.europa.eu/sites/default/files/dfu/EASA_J-News_December_2018.pdf
- Graphics Pro website
https://graphics-pro.com/feature/wrapping-aircraft/
- FAA ( 2022, Aug) Small Airplane Standards Branch Non-Basic Classification Criteria and Safety Emphasis Items List, 2260 V1.1 Vinyl Covering Shrink Wraps on Exterior of Part 23 Airplanes, Gliders, and Airships.
https://www.faa.gov/sites/faa.gov/files/2022-08/ANAC_Non-Basic_Criteria_List_r2.pdf